Setting Up Best Practices
Having your basic preventive maintenance plan up and running is great, but to ensure the long-term success of this transition and enjoy all the benefits that come with it, we recommended documenting your company’s procedures that will be regularly used by your maintenance staff.
This is yet another instance in which CMMS proves to be a real asset by becoming a central hub where all asset documentation and procedures are stored.
And the more it’s in use, the more up to date and accurate is the data that is being stored. This can later be used for future staff training and as a way to monitor your program’s success. Any deficiencies or missteps will be easily identified and it will make evaluating and updating procedures easier as new information and situations arise.
Let’s check up on the most common procedures and practices you want to define.
Creating, responding to and closing out work
Effectively managing tasks is an integral part of any maintenance strategy. For tasks to be dispositioned, assigned, and prioritized in an effective manner, your whole maintenance team needs to be on the same page.That is what you have to define:
- Who is responsible for creating new unscheduled tasks?
- Who on your maintenance team is responsible for what type of work?
- Who will be reviewing open/closed work to make sure things are getting done?
- Whose responsible for reassigning work as technicians become unavailable/available?
- What are the criteria for escalation and/or emergency identifiers?
Limble, for example, will send every technician a notification when they are assigned to a particular work order. If you can equip your team with an appropriate number of handheld devices, through a mobile CMMS, they will also be able to seamlessly communicate and cooperate on bigger maintenance tasks, as well as update the progress of particular work orders at any time.

Reporting problems and work requests
Having a systematic way to report issues or abnormal performance will ensure that anyone performing inspections will be monitoring the proper areas that can cause potential issues. More importantly, it will help to track budding defects in the system’s operation so small anomalies can be caught and quickly resolved.Problems are usually reported in one of two different manners. Either by your maintenance staff that can report a problem through your CMMS’s mobile app. Or by non-maintenance staff which can report a problem through a Work Request portal.
Showing non-maintenance staff how to submit a work request is a large time-saver but only works if it is implemented and documented.
Recording critical information
Each time an inspection takes place, anyone performing the inspection should record critical data like date, time, temperature and pressure levels, or any other critical information that determines the state of the asset in question.Depending on the type of asset this information could prove extremely beneficial in the future.
Identifying how your inventory will be kept up to date
An up to date inventory is incredibly important as it will make sure when something breaks, you have the needed materials to fix it.You can either perform manual audits of your inventory or have your CMMS automatically keep track of you as parts are used.
When work is closed out in a CMMS, attached used parts will automatically be subtracted from your inventory records. This can ease the burden of having to manually check parts and update spreadsheets.
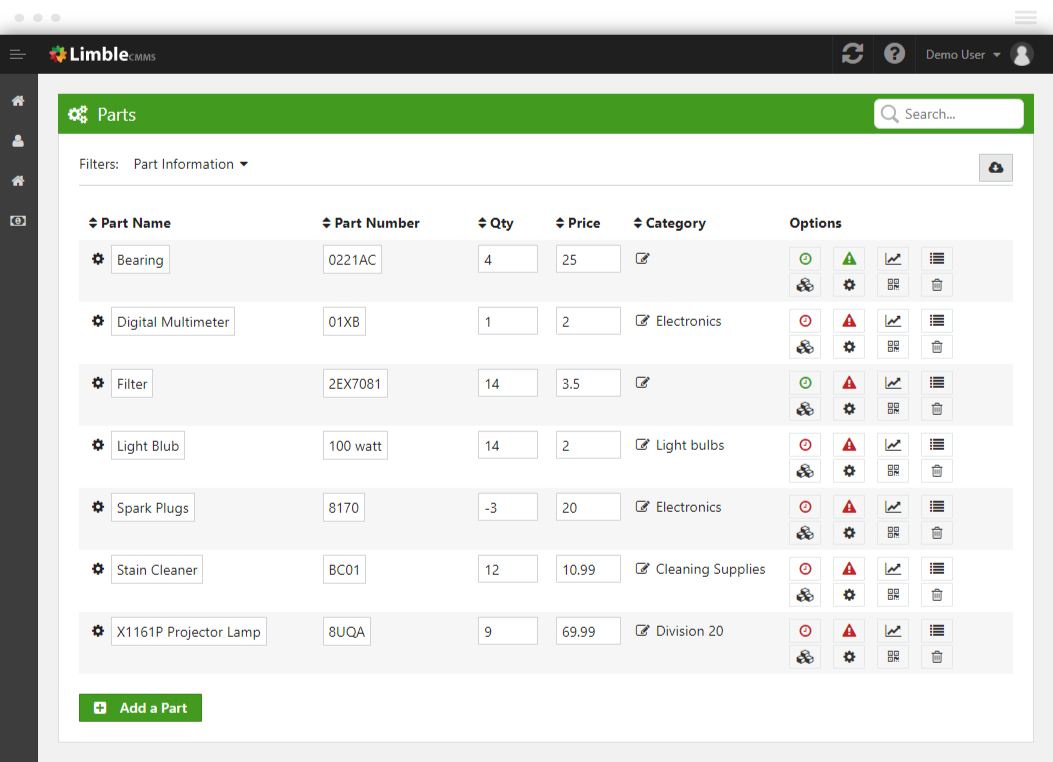
Another feature you might find useful is the option to have set thresholds for your parts and instruct CMMS to send you an alert whenever the number of spare parts in stock falls below that threshold.
Managing your vendors
Having everything running smoothly means that you can quickly get in touch with all of your outside contractors.According to the recent Plant Engineering’s Maintenance survey, 74% of facilities outsource at least one part of their maintenance operations. The main reasons being lack of time and manpower and too many specialized skills required.An approved or qualified vendor list should be readily available complete with each asset-specific identifier (equipment ID, serial/make/model number etc.), account numbers, contractors’ email address, and all phone numbers.
Other helpful information includes hours of operation, separate after hour service call procedures, Account Representative’s name or the name of specific service personnel with direct contact information and any notes that are needed to place a service call with minimal hassle.
Your blog is filled with unique good articles! I was impressed how well you express your thoughts.
Trả lờiXóaOne Nation One Health Card | Health Id Card
Thank you for posting such a great article! It contains wonderful and helpful posts. Keep up the good work
Trả lờiXóaJnanaBhumi Portal - AP State Portal, Jnanabhumi Scholarship - Online Apply, Application Status Check, Renewal Procedure